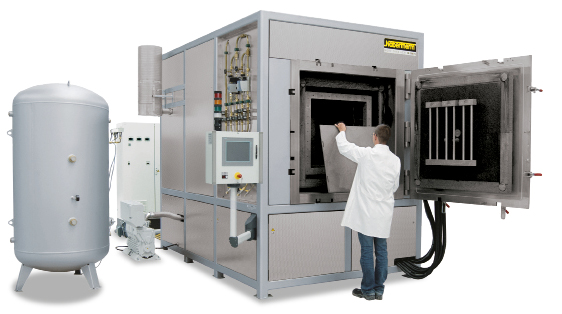
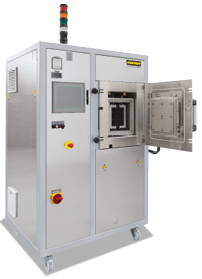
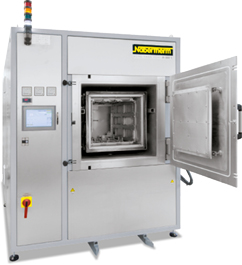
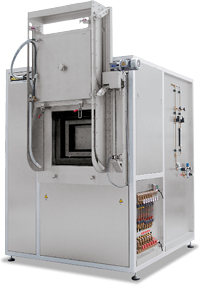
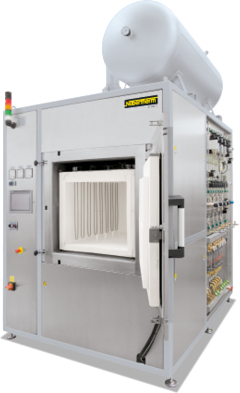
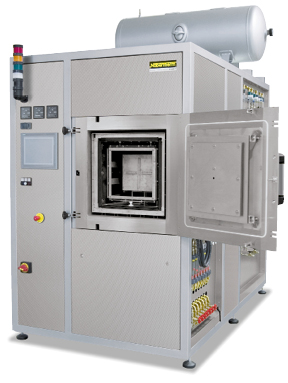
05 ตุลาคม 2566
ผู้ชม 2343 ผู้ชม
Retort furnace VHT 500/22-GR H2 with CFC-process box and extension package for operation under hydrogen |
![]() |
![]() |
![]() |
The compact retort furnaces of the VHT product line are available as electrically heated chamber furnaces with graphite, molybdenum, tungsten or MoSi2 heating. A wide variety of heating designs as well as a complete range of accessories provide for optimal retort furnace configurations even for sophisticated applications. The vacuum-tight retort allows heat treatment processes either in protective and reaction gas atmospheres or in a vacuum, subject to the individual furnace specs to 10-5 mbar. The basic furnace is suited for operation with non-flammable protective or reactive gases or under vacuum. The H2 version provides for operation under hydrogen or other flammable gases. Key of the specification up is a certified safety package providing for a safe operation at all times and triggers an appropriate emergency program in case of failure. Alternative Heating Specification In general the following variants are available wit respect to the process requirements: VHT ../..-GR with Graphite Insulation and Heating
VHT ../..-MO or VHT ../..-W with Molybdenum or Tungsten Heating
VHT ../..-KE with Fiber Insulation and Heating through Molybdenum Disilicide Heating Elements
|
![]() Schematic presentation of a cold-wall retort furnace with additional equipment 1 Retort 2 Heating 3 Insulation 4 Gas management system 5 Vacuum pump 6 Cooling water distribution 7 Controls 8 Integrated switchgear 9 Heating transformer 10 Charging frame inside the inner process chamber |
![]() Retort furnace VHT 8/16‑MO with automation package |
![]() Retort furnace VHT 100/16‑MO with automation package |
Basic version
|
Retort furnace VHT40/22-GR with motor-driven lift door and front frame for connection to a glovebox |
Heat treatment of copper bars under hydrogen in retort furnace VHT 8/16-MO |
Thermocouple, type S with automatic pull-out device for precise control results in the low temperature range |
Turbo-molecular pump |
Additional equipment housing/heater
Additional equipment gas management system
Additional equipment vacuum
Additional equipment cooling
Additional equipment for controls and documentation
|
![]() Single-stage rotary vane pump for heat treatment in a rough vacuum to 5 mbar |
![]() to 10-2 mbar |
![]() |
![]() six charge supports |
Process Box for Debinding in Inert Gas If there is no way to avoid the escape of small amounts of residual binder during the process, even in the VHT furnace, the retort furnace should be designed to meet this contingency. The furnace chamber is equipped with an additional process box that has a direct outlet to the exhaust gas torch through which the exhaust gas can be directly vented. This system enables a substantial reduction in the amount of furnace chamber contamination caused by the exhaust gases generated during debinding. Depending on the exhaust gas composition the exhaust gas line can be designed to include various options.
|
|||
Retort furnace VHT100/15-KE H2 with fiber insulation and extension package for operation under hydrogen, 1400°C |
Retort furnace VHT40/16-MO H2 with hydrogen extension package and process box |
![]() Gas management system |
H2 Version for Operation with Hydrogen or other Reaction Gases
In the H2 version the retort furnaces can be operated under hydrogen or other reaction gases. For these applications, the systems are additionally equipped with the required safety technology. Only certified and industry proven safety sensors are used. The retort furnaces are controlled by a fail-safe PLC control system (S7-300F/safety controller).
Additional equipment
|
![]() |
ขอใบเสนอราคา |
---|
Reference Customer (กดที่โลโก้ เพื่อดูเว็บไซต์ของลูกค้าที่สั่งซื้อสินค้ากับทางบริษัท) | ||||
อยู่ในระหว่างอัพเดทข้อมูล... |